Choosing the ideal casters for your specific needs is critical—and often, it’s a complex decision. This definitive guide demystifies the process, shining a spotlight on these essential but frequently overlooked components of modern mobility. Casters are foundational to the smooth operation of everything from office furniture to industrial equipment. The perfect caster choice empowers effortless transit, safeguards valuable materials, and upholds the integrity of your workspaces. Whether it’s reducing physical strain for employees, or ensuring precision handling of sensitive cargo, this guide breaks down key considerations, such as load capacity, wheel material, and caster type, to help you make an informed decision. Explore insights that strike a balance between operational efficiency and workplace safety, and navigate through the extensive range of options with confidence. Discover how to expertly select casters that optimize functionality, longevity, and overall performance—whether you’re outfitting a new office chair or engineering a complex assembly line system.
1. Understanding Load Capacity
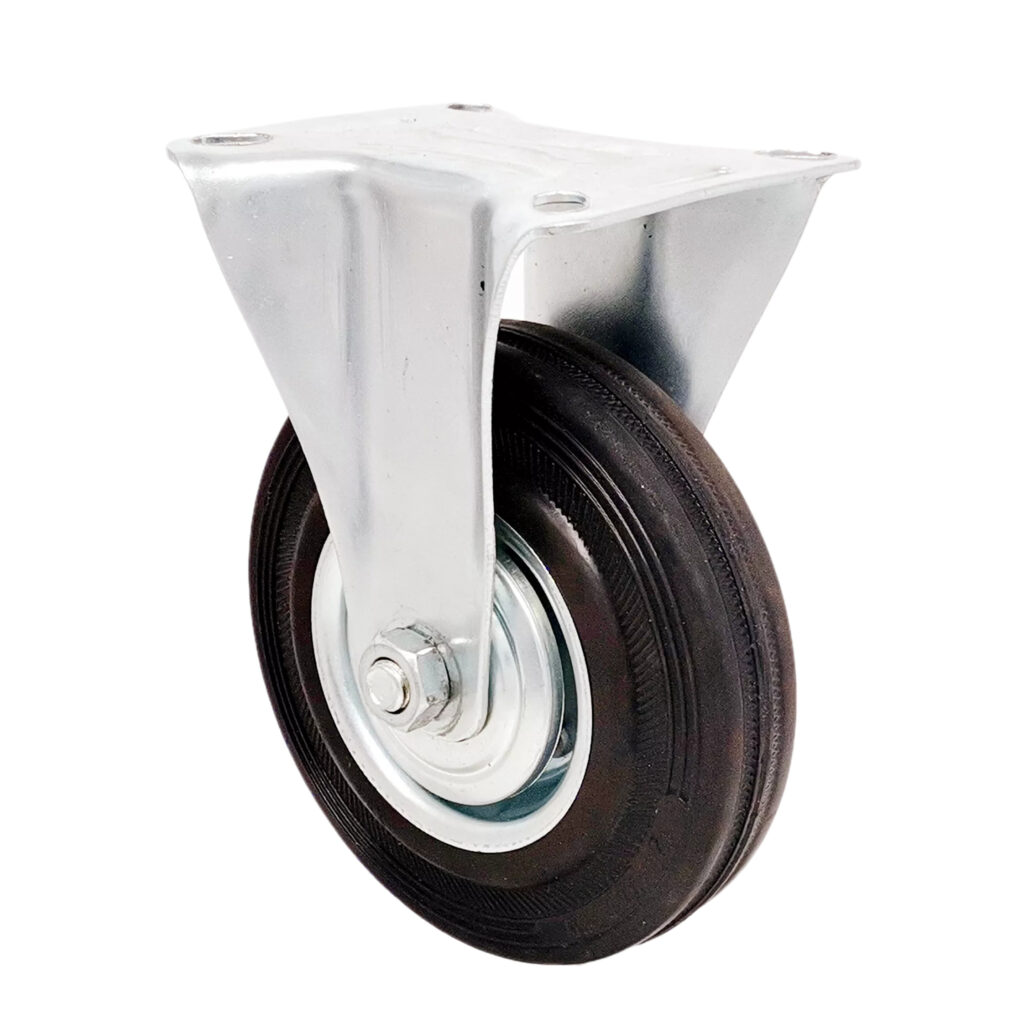
When selecting casters, understanding and accurately determining the load capacity is paramount. The load capacity is not merely about the static weight of the cargo but includes the complete weight distribution that the casters will support. This encompasses the weight of the equipment, the payload, and additional forces that might affect caster performance during dynamic movement.
Calculating the appropriate load capacity requires factoring in the total weight and dividing it by the number of casters to be used. However, it’s advisable to add a safety margin beyond the bare minimum to account for unforeseen overloads and to enhance the longevity of the casters. Remember that dynamic loads can vastly differ from static ones due to forces exerted by acceleration, deceleration, and maneuvering.
Manufacturers typically rate casters for both static and dynamic loading, and understanding the distinction is crucial. Dynamic load capacity can be affected by factors such as the frequency of movement, travel distances, the type of flooring surface, as well as the velocity at which the casters will move. Quick turns and irregular terrains can induce additional stress, thus necessitating a higher load rating.
Taking the time to assess the conditions under which the casters will operate and allowing for a buffer above the actual load will help prevent premature wear, enhance safety, and preserve the integrity of both casters and floors. This careful consideration will ensure that the selected casters can handle the given application’s demands, minimize the risk of failure, and secure a safe environment for both the transported goods and the handlers.
2. Floor Compatibility and Wheel Materials
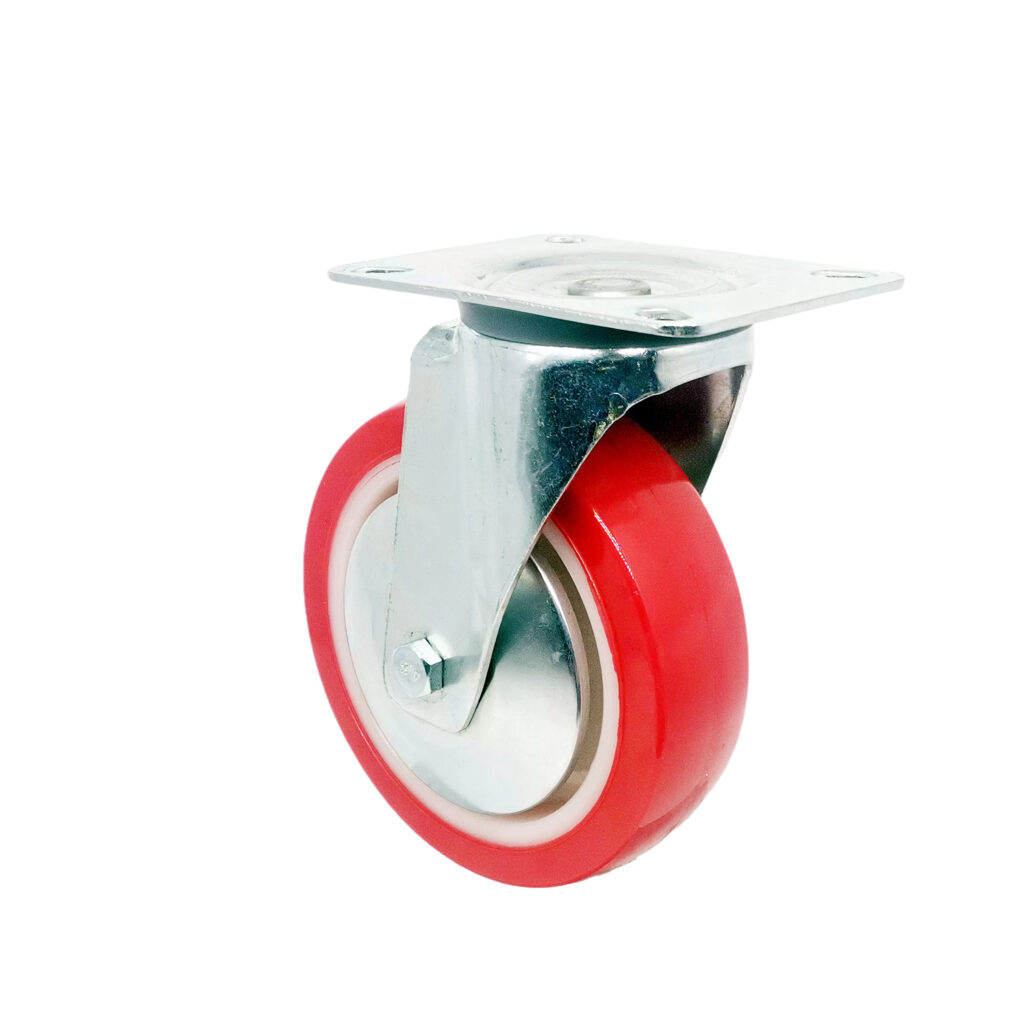
The interaction between the wheel material and the floor is a major factor in determining caster performance. The right combination minimizes wear on both the wheel and the floor, reduces noise, and provides the desired ease of movement. Considerations such as floor texture, presence of obstacles like thresholds or floor joints, and environmental factors like the presence of oils, chemicals or extreme temperatures are critical in choosing the best wheel material. Common materials include nylon, polyurethane, and rubber, each with distinct advantages. Nylon wheels are tough and work well on smooth, hard surfaces, but can be noisy. Polyurethane wheels offer a balance between durability and floor protection, perform well under varying loads, and are resistant to many chemicals and solvents. Rubber wheels are quieter and protect floors from marks but can degrade if exposed to certain chemicals or intense sunlight.
3. Fixed vs. Swivel vs. Braked Casters
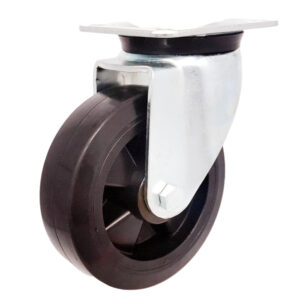
When considering the mobility of casters, one must evaluate the operational needs to select the most appropriate type. Fixed casters offer a linear motion path, optimal for straightforward routes without the need for intricate navigation. Their rigidity provides stability and is ideal for transporting consistently heavy loads along predefined paths.
Swivel casters add a layer of versatility with their 360-degree rotating mounts, enabling equipment to maneuver with ease around obstacles and tight corners. The initial force required to pivot and redirect these casters is offset by their operational flexibility, making them the caster of choice for dynamic environments where directional freedom is paramount.
For situations that demand both movement and stationary control, braked casters are the key. They include mechanisms that lock the wheel, and in some models, the swivel action as well, ensuring that equipment remains firmly in place when required. Easy-to-use locks, often activated by foot, prevent rolling or turning, which is especially crucial on slopes or during precision tasks.
Understanding the distinct characteristics and functionalities of fixed, swivel, and braked casters allows one to tailor the caster choice to the specific needs of the application. The decision will hinge on the balance between straight-line stability and the need for agile, multi-directional movement, combined with the option for secure, stationary positioning.
4. Specialty Casters for Unique Needs
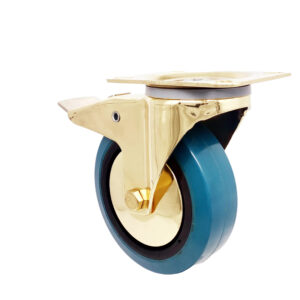
In environments with precise requirements, specialty casters deliver tailored solutions. Stainless steel casters ensure cleanliness and corrosion resistance for food processing or medical application. Casters designed for high-temperature environments, such as autoclaves or bakeries, use materials capable of withstanding prolonged exposure to extreme heat. ESD casters are outfitted with conductive materials to safely discharge any build-up of static electricity, critical in electronics manufacturing or explosive environments. Casters for clean rooms are designed to minimize particle shedding and withstand sterilization processes, ensuring they do not compromise the sterile environment.
5. Making the Right Choice for Your Situation
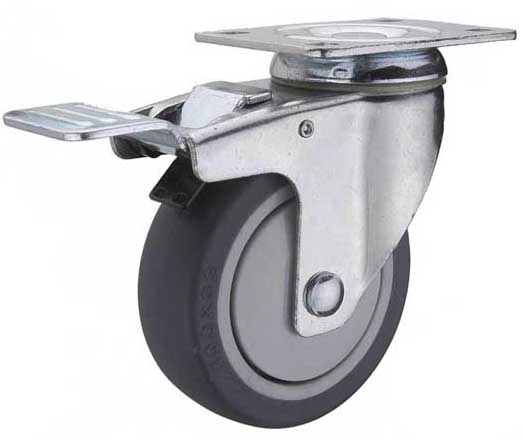
The right caster can be the difference between smooth operations and a logistical nightmare. Selection is not simply about picking a wheel; it’s about understanding the unique needs of your equipment, the environment it will navigate, the loads it will bear, and the people who will interact with it. Start by evaluating the weight distribution your casters will need to support and consider the various floor conditions they will encounter. Will they glide over polished office floors or traverse rugged warehouse terrain? Maneuverability is another critical factor; will your casters need to make sharp turns or fit into tight spaces? Swivel casters might be ideal in such scenarios, while fixed casters could suffice for straight-line paths.
Equally important are ergonomic considerations. Operations that require frequent movement can benefit from casters designed to reduce the force needed to push or pull. Ergonomically designed casters can significantly decrease workplace strain and related injuries.
Selecting your casters is only the beginning. Good maintenance practices are imperative to extend their life and ensure continued performance. This includes frequent inspections for damage or wear, timely lubrication of bearings, and cleaning debris from wheel treads to avoid traction loss. Occasionally, the application of thread-locking adhesives may be necessary to keep fasteners tight in high-vibration environments. By following these steps, you secure not just a successful initial fit but also ongoing reliability and safety for the lifespan of your mobile equipment.
6. Conclusion
The right casters merge seamless mobility with robust functionality. They are a pivotal aspect of logistical operations, and selecting the right one can be a significant determinant of efficacy. This guide intended to provide you with the knowledge to select the most appropriate casters for your application.