When you buy casters, you need to know how good they are and how long they’ll last. Casters are used in a lot of different industries, from healthcare to heavy manufacturing, and if you buy the wrong ones, you can have equipment failure, operational inefficiencies, or even safety hazards. People often don’t know which tests are important to make sure the casters they buy meet industry standards.
There are eight crucial tests for casters that buyers need to be aware of, including hardness tests, load capacity tests, and brake fatigue tests. Understanding these tests ensures that the casters you choose are durable, reliable, and safe for the intended use.
Let’s go through each test and talk about why it’s important when you’re buying casters.
Key Caster Testing Standards
1. Hardness Test
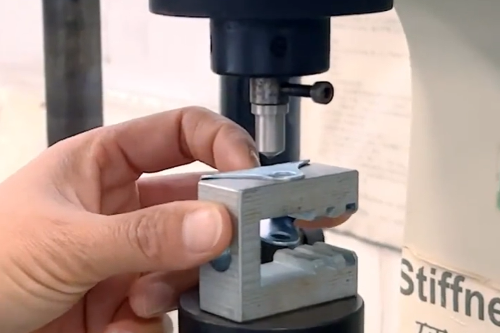
- What it measures: The hardness test determines the caster’s ability to resist surface indentation, wear, and deformation under pressure. This test evaluates how the caster material withstands repeated impacts, heavy loads, and friction. Hardness is usually measured using a durometer, which gauges the material’s resistance to indentation.
- Why it matters: A higher hardness rating means better durability, particularly in environments where casters will be subjected to harsh conditions, such as heavy machinery or uneven surfaces. If a caster lacks hardness, it may deform, flatten, or crack under weight or impact, leading to operational failure or accidents. Harder casters ensure smoother movement, less rolling resistance, and reduced wear on both the caster and the floor surface, minimizing long-term maintenance costs.
- Industry applications: Hardness tests are essential in heavy manufacturing industries, automotive production, and warehouses, where casters encounter frequent impacts, heavy loads, or abrasive surfaces. For example, in an automotive assembly line, casters must bear the weight of parts, tools, and equipment while resisting constant wear. If these casters don’t pass the hardness test, they might crack or deform, leading to downtime and potential safety hazards.
2. Wear Resistance Test
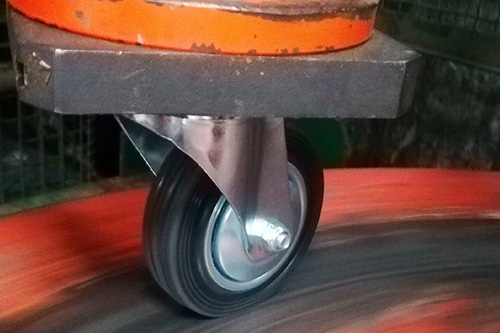
- What it measures: The wear resistance test evaluates the caster’s ability to withstand abrasion and continuous friction over time. It simulates real-world conditions by repeatedly running the caster over abrasive surfaces, tracking its resistance to gradual degradation, material loss, or damage. This test measures the longevity of the caster’s surface material and its ability to retain its original shape and function.
- Why it matters: Casters in high-traffic environments such as hospitals, warehouses, and factories are constantly in use. Poor wear resistance can result in casters degrading quickly, leading to higher replacement costs, equipment downtime, and the potential for accidents if a caster fails mid-operation. Wear-resistant casters not only last longer but also maintain consistent performance, reducing the risk of equipment malfunction due to worn-out wheels.
- Industry applications: Wear resistance is especially crucial in environments where casters are exposed to rough or uneven surfaces, such as distribution centers, healthcare facilities, and industrial plants. For example, in a hospital, medical equipment like beds and gurneys must be easily maneuvered across both smooth hallways and rough outdoor surfaces. Casters with poor wear resistance can wear down quickly, becoming difficult to roll and increasing the risk of patient or equipment mishandling.
3. Load Capacity Test
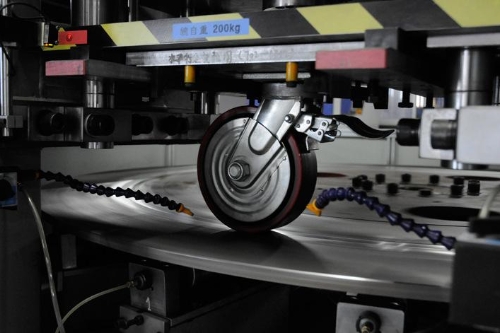
- What it measures: The load capacity test determines how much weight a caster can support before it deforms, fractures, or fails. This test simulates maximum load conditions by applying increasing weight to the caster, assessing its structural integrity and functionality under stress. Load capacity is crucial for preventing caster failure under heavy loads.
- Why it matters: In environments where casters must carry heavy equipment or materials, failure to meet load capacity requirements can lead to catastrophic results, including accidents, equipment damage, and operational inefficiencies. A caster that deforms or breaks under weight can cause costly delays, injuries, or damage to the product it supports. Selecting casters with the appropriate load rating ensures safety, functionality, and longevity.
- Industry applications: Industries such as logistics, transportation, and manufacturing heavily rely on casters to transport heavy loads. For example, casters on pallet jacks or warehouse carts must bear the weight of goods ranging from hundreds to thousands of pounds. If these casters fail, it can lead to damaged products, unsafe working conditions, and lost productivity.
4. Long-Distance Walking Test
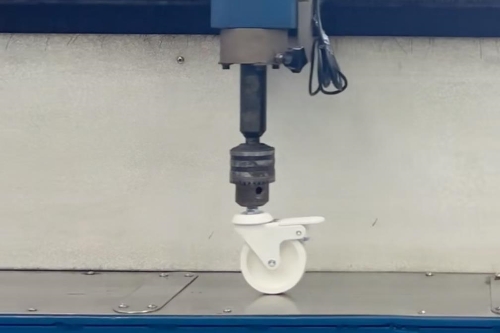
- What it measures: The long-distance walking test simulates extended use by rolling the caster over long distances, often across various surface types, to evaluate its durability and rolling efficiency. This test measures how well the caster maintains its structural integrity, smooth rolling motion, and resistance to wear after prolonged use.
- Why it matters: Casters that are used in environments with long corridors or large spaces, such as airports, warehouses, and hospitals, need to maintain performance over extended distances. Failure to pass this test can result in uneven rolling, increased resistance, or mechanical failure, making it difficult to move equipment efficiently. Casters that endure long-distance walking tests are more reliable and require less frequent replacement, reducing costs and downtime.
- Industry applications: This test is vital for industries like logistics, healthcare, and manufacturing, where equipment or carts are frequently moved over long distances. For example, in a large hospital, medical carts and gurneys need casters that can handle constant movement without wearing down or causing operational issues. Casters that fail this test may become stiff, noisy, or unstable, disrupting operations.
5. Salt Spray Test
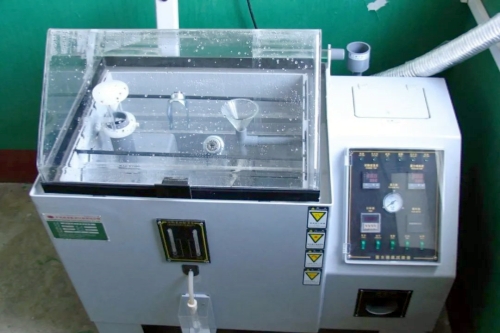
- What it measures: The salt spray test measures the caster’s resistance to corrosion when exposed to salty or humid environments. This test simulates conditions that mimic coastal or high-humidity regions, where casters are likely to encounter moisture, salt, or chemicals that can cause rusting. The test typically involves exposing the caster to a saltwater mist for extended periods to assess its corrosion resistance.
- Why it matters: Corrosion weakens the structural integrity of casters and reduces their lifespan. Rust buildup can cause the caster to seize up, making equipment difficult to move and increasing the risk of failure during use. Casters with high corrosion resistance will last longer in environments prone to moisture, preventing frequent replacements and ensuring smooth operation.
- Industry applications: The salt spray test is essential for casters used in outdoor environments, coastal regions, marine industries, and warehouses where humidity is high. For example, in a shipping dock near the coast, carts and equipment are constantly exposed to salty air and moisture. Casters that fail this test will rust and deteriorate quickly, leading to higher maintenance costs and potential operational delays.
6. Brake Fatigue Test
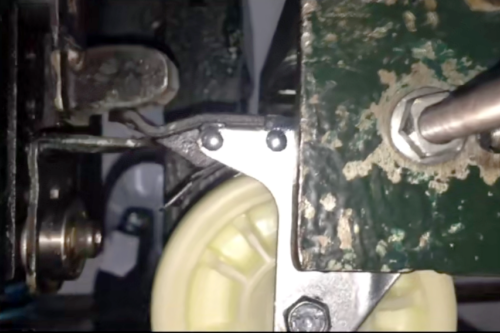
- What it measures: The brake fatigue test evaluates the durability and effectiveness of a caster’s braking system over repeated uses. This test subjects the caster’s brake to multiple cycles of engagement and release, simulating frequent use in real-world applications. It checks whether the brake continues to function properly after repeated activation and ensures that it holds the caster securely in place.
- Why it matters: In environments where equipment must remain stationary for extended periods, such as hospitals, laboratories, or assembly lines, reliable brakes are crucial. A failed brake can lead to equipment rolling away unexpectedly, causing accidents or damaging sensitive equipment. Casters that pass the brake fatigue test provide peace of mind by ensuring that the brake system remains effective even after extensive use.
- Industry applications: Brake fatigue tests are vital in industries such as healthcare, manufacturing, and hospitality, where equipment must remain stationary in specific locations. For example, in a medical setting, a brake failure on a hospital bed or medication cart could lead to a dangerous situation. Casters that can withstand brake fatigue ensure safety and stability in critical environments.
7. Electrical Resistance Performance Test
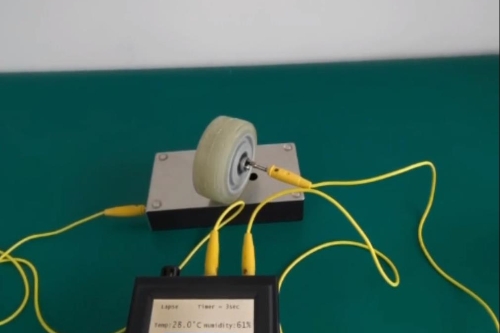
- What it measures: This test measures how well a caster can resist the buildup of static electricity. In environments sensitive to static discharge, such as electronics manufacturing or clean rooms, static electricity can damage sensitive equipment or create hazardous conditions. The electrical resistance test ensures that the caster can safely discharge electrical buildup, preventing static-related accidents or equipment failures.
- Why it matters: In industries where static discharge can cause serious damage or safety risks, such as semiconductor manufacturing or laboratories handling flammable substances, it is crucial to use casters that prevent static buildup. A failure to pass this test could result in damaged products, data loss, or even fires. Casters with proper electrical resistance reduce the risk of static buildup and ensure a safe working environment.
- Industry applications: Electrical resistance testing is particularly important in clean rooms, electronics manufacturing facilities, and hospitals, where static discharge can interfere with sensitive medical or electronic equipment. For example, in a clean room environment where semiconductors are produced, even a small static discharge can destroy delicate electronic components, leading to costly downtime and production losses.
8. Service Life Test
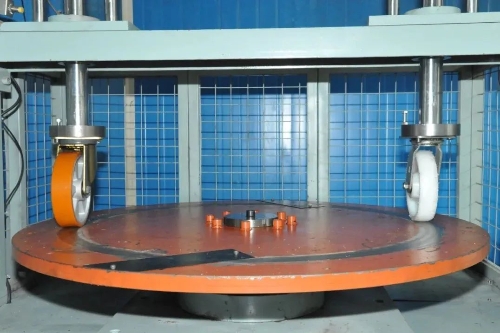
- What it measures: The service life test assesses the overall longevity of the caster by subjecting it to repeated cycles of movement, stress, and load-bearing activities. This test simulates long-term use to estimate how long the caster will last before it needs to be replaced. It measures the caster’s ability to withstand continuous stress without significant degradation.
- Why it matters: Knowing the estimated service life of a caster helps industries plan for maintenance, reducing unexpected breakdowns and minimizing downtime. Casters that pass the service life test are more likely to offer a longer working life, reducing the frequency of replacements and lowering operational costs. Reliable casters are crucial for industries that operate under strict schedules and can’t afford unplanned equipment failure.
- Industry applications: The service life test is critical for industries that rely on durable, long-lasting casters, such as manufacturing, logistics, and healthcare. For example, in a factory with 24/7 operations, equipment downtime due to caster failure can lead to production delays and increased costs. Casters that pass this test help minimize maintenance interruptions and ensure continuous operation.
Practical Questions for Buyers
What are the Best Tests to Ensure Caster Wheels are Durable?
To ensure caster wheels are durable, several tests are essential. The Hardness Test, Wear Resistance Test, and Service Life Test each play a role in determining a caster’s ability to withstand demanding conditions. These tests are particularly important in industrial and high-use environments where durability is critical.
How Can I Test the Load Capacity of Caster Wheels?
Testing a caster wheel’s load capacity involves subjecting it to increasing amounts of weight until deformation or breakage occurs. This Load Capacity Test ensures that casters can handle the specified weight without risking accidents or equipment damage. It’s vital for industries where heavy loads are frequently moved.
What are the Most Reliable Brands for High-Quality Caster Wheels?
Several brands specialize in high-quality caster wheels that meet rigorous industry standards. Reliable manufacturers often adhere to ICWM (Institute of Caster and Wheel Manufacturers) or ISO (International Organization for Standardization) certifications, ensuring their products undergo comprehensive testing for durability and performance.
How Do I Test the Swiveling Motion of Caster Wheels?
The swiveling motion of casters is tested through the Long-Distance Walking Test, which checks how smoothly a caster rotates during extended use. This test ensures that the caster maintains its ability to swivel and rotate freely without excessive resistance, wear, or sticking, which is vital for mobile equipment.
Conclusion
Understanding these tests can make a big difference when you’re buying casters. Each test addresses a different aspect of performance—whether it’s the caster’s ability to handle heavy loads, resist corrosion, or swivel smoothly. By paying attention to these tests, you can make sure you’re buying casters that will last and keep your equipment moving safely and efficiently for years to come.