How Casters Are Made?
Casters are vital components in everyday products like office chairs, trolleys, and machinery. But have you ever wondered how these small wheels are made? The process is more intricate than you might think. From material selection to molding, each step ensures durability and smooth movement.
Casters are created using a precise process involving nylon wheel inserts placed in an injection molding press. This machine melts rubber, injects it into the mold, and solidifies the material. After cooling for around two and a half hours, the edges of the wheels are smoothed for optimal performance.
Now that we know the basics of caster production, let's dive deeper into the materials used and how various caster types are made for specific needs.
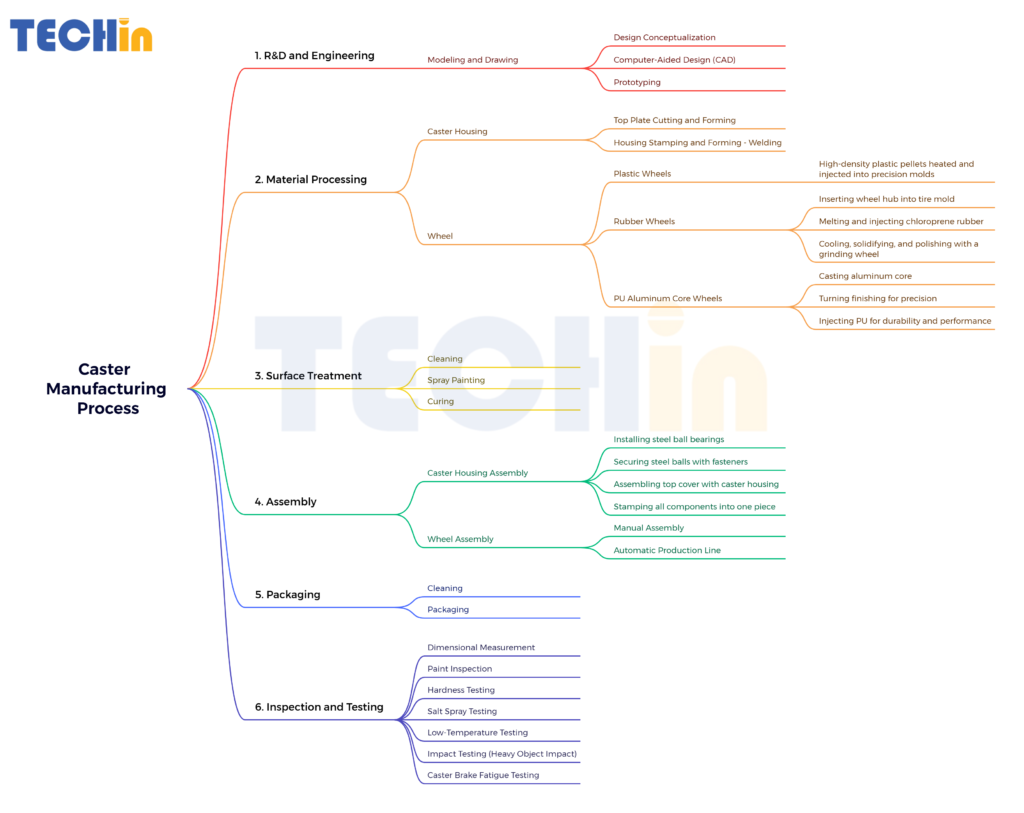
Looking for reliable caster manufacturers?
1. R&D and Engineering
Modeling and Drawing
The manufacturing process begins with research and development. Engineers utilize advanced CAD software to model and draw detailed designs for the caster wheels, ensuring they meet specific requirements for various applications. This stage involves:
- Design Conceptualization: Brainstorming and conceptualizing the initial design based on intended use, load capacity, and environmental conditions.
- Computer-Aided Design (CAD): Creating precise 3D models and technical drawings that serve as blueprints for manufacturing.
- Prototyping: Developing prototypes to test the design’s functionality and durability, making necessary adjustments before mass production.
2. Material Processing
Caster Housing
- Top Plate Cutting and Forming: Precision cutting of steel plates is followed by forming processes to create the top plate, ensuring it meets exact specifications.
- Housing Stamping and Forming – Welding: Stamping machines form the housing by pressing the steel into molds, followed by welding to assemble different parts, ensuring a strong and durable structure.
Wheel:
- Plastic Wheels: High-density plastic pellets are heated and injected into precision molds to create wheels with consistent quality and dimensions.
- Rubber Wheels: The wheel hub is inserted into the tire mold. Chloroprene rubber is melted and injected into the mold. After forming, the wheel is cooled, solidified, and polished with a grinding wheel for a smooth finish.
- PU Aluminum Core Wheels: Aluminum cores are die-cast and undergo turning finishing for precision. Polyurethane (PU) is then injected into the mold containing the aluminum core, combining the strength of aluminum with the flexibility of PU.
3. Surface Treatment
Surface Treatment: After the caster housing is welded, it undergoes surface treatment to enhance durability and aesthetics:
-
- Cleaning: The housing is cleaned to remove any contaminants that might affect the paint adhesion.
- Spray Painting: High-quality paint or coatings are applied using automated spray systems, providing a uniform layer that protects against rust and corrosion.
- Curing: The painted housing is baked in an oven to cure the paint, ensuring a hard, durable finish.
4. Assembly
Caster Housing Assembly
- Installing Steel Ball Bearings: Steel balls are inserted into the housing to facilitate smooth swiveling motion.
- Securing Steel Balls with Fasteners: Steel fasteners are used to secure the steel balls in place, ensuring they remain firmly seated within the housing.
- Assembling the Top Cover with the Caster Housing: The top cover is installed, and all components are stamped into one cohesive piece, forming a robust and reliable caster housing.
6. Inspection and Testing
Quality control is critical in the manufacturing process. Each caster undergoes rigorous inspection and testing to ensure it meets industry standards:
-
- Dimensional Measurement: Ensuring all components meet precise specifications using calipers and micrometers.
- Paint Inspection: Visual and automated inspections check the quality of the surface coating for uniformity and adherence.
- Hardness Testing: Verifying the material hardness to ensure durability and resistance to wear.
- Salt Spray Testing: Simulating corrosive environments to test the caster’s resistance to rust and corrosion.
- Low-Temperature Testing: Ensuring the casters function correctly in cold conditions, critical for certain applications.
- Impact Testing (Heavy Object Impact): Dropping heavy weights onto the casters to test their durability and ability to withstand impact forces.
- Caster Brake Fatigue Testing: Repeatedly engaging and disengaging the brake mechanism to test its longevity and reliability under repeated use.
People Also Ask
What materials are typically used for caster wheels?
Caster wheels are made from various materials, each offering distinct advantages:
- Cast Iron/Semi-Steel: Abrasion-resistant and long-wearing, these wheels can withstand extreme temperatures and are suitable for high-capacity applications and environments with chemicals, oil, grease, and metal chips.
- Rubber: Available in hard and soft varieties, rubber wheels offer good traction, floor protection, and quiet operation. They are resistant to most chemicals and suitable for various floor types.
- Thermoplastic Rubber (TPR): Precision molded and mechanically locked to a durable polyolefin core, these wheels offer excellent performance and longevity.
- Nylon/Plastic: These wheels offer easy rolling, chemical resistance, and high load capacity. They are suitable for harsh chemical environments and can have very high load capacities.
- Polyurethane: Capable of carrying higher loads than rubber and lasting longer, polyurethane wheels offer floor protection and quiet operation.
- Steel: Used for caster components like forks, axles, plates, and stems due to its strength and durability. It can be treated with various finishes for corrosion resistance.
- Pneumatic/Solid/Semi-Pneumatic: These wheels work well on rough and uneven surfaces, providing the best cushioning. They are preferred for outdoor applications on soft surfaces.
When choosing a caster material, consider factors such as the required load capacity, floor type, noise levels, chemical resistance, and operating environment. Each material has its own advantages and is suited for specific applications.
How do different manufacturing processes affect the quality of caster wheels?
The quality of caster wheels is heavily influenced by the manufacturing process:
- Injection Molding: Ensures precise shapes and uniformity, reducing the likelihood of defects. This process is ideal for producing large quantities of wheels with consistent quality.
- Casting: Produces strong, durable components by pouring molten material into molds. It is commonly used for making metal parts like aluminum cores.
- Stamping and Welding: Used for creating the caster housing, these processes ensure robust construction capable of withstanding heavy loads.
What are the advantages of using injection molding for caster wheels?
Injection molding offers several advantages:
- Precision: The process produces wheels with accurate dimensions and consistent quality.
- Efficiency: Injection molding is highly efficient, making it ideal for large-scale production.
- Material Variety: It allows the use of various materials, including high-strength plastics and composites.
- Cost-Effective: The process is cost-effective for mass production, reducing per-unit costs while maintaining high quality.
What are the key steps in the caster assembly process?
The caster assembly process involves several key steps:
- Installing the Steel Ball and Fasteners: Ensuring smooth swiveling motion by securing steel balls in place.
- Assembling the Caster Housing: Combining all components to form a robust frame.
- Attaching the Wheels: Using manual or automated processes to securely attach the wheels to the housing.
- Inspection and Testing: Conducting rigorous quality control checks to ensure each caster meets industry standards.
- Cleaning and Packaging: Preparing the finished casters for distribution by cleaning and packaging them securely.
Summary
By understanding the comprehensive process of manufacturing caster wheels, buyers can better appreciate the intricacies involved and make informed purchasing decisions. Ensuring quality at each step is essential for producing reliable and durable caster wheels.
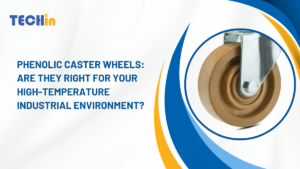
Phenolic Caster Wheels: Are They Right for Your High-Temperature Industrial Environment?
Let’s face it: some industrial environments are demanding. High heat from autoclaves or baking lines can quickly degrade standard caster wheels. Phenolic caster wheels are
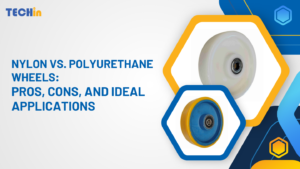
Nylon vs. Polyurethane Wheels: Pros, Cons, and Ideal Applications
Picking the right wheels for your cart, chair, or industrial equipment feels like a small decision, right? Wrong. Get it wrong, and you’re stuck with
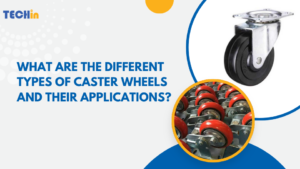
What Are the Different Types of Caster Wheels and Their Applications?
Choosing the right caster wheel is crucial for safety, efficiency, and performance. The wrong choice can result in floor damage, equipment instability, or premature wear.