Introduction
In the world of mobility equipment, understanding how much weight a caster can hold is essential for ensuring functionality, safety, and longevity. From industrial applications to medical environments, knowing caster load capacity helps buyers make informed decisions, protecting equipment, operators, and flooring. In this guide, we’ll explore the factors affecting caster load capacity, how to calculate it, and tips for choosing the best caster for your needs.
The Concept of Load Capacity
The load capacity of casters is a fundamental concept in mobility and transportation that defines how much weight a caster can safely support. This is a critical aspect of caster selection, as it ensures not only the functionality of the equipment but also the safety of the users and longevity of the application. Understanding the load capacity involves grasping the load rating, the impact of caster size on weight capacity, and the importance of load distribution among casters.
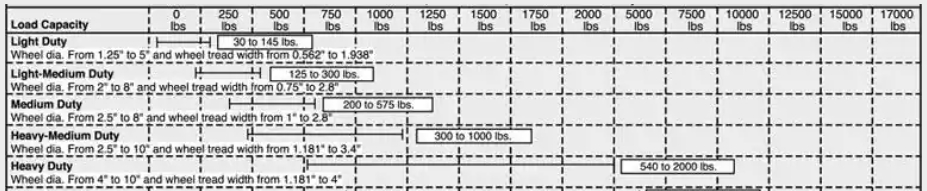
Understanding Load Rating
The load rating of a caster refers to the maximum weight that it can safely carry. Determined through comprehensive testing and adherence to strict industry standards, this rating is crucial for users to understand before implementing the casters into their designs. It’s essential to take into account that the stated load rating is given per individual caster. For instance, if a piece of equipment is structured to be moved on four casters, then the total weight capacity would be four times the load rating of one caster, assuming equal load distribution.
It is also necessary to differentiate between the static load capacity, which is the weight the caster can carry when not moving, and the dynamic load capacity, which is typically lower and represents the weight the caster can carry when rolling.
The Impact of Caster Size on Weight Capacity
The size of the caster, especially the wheel diameter, greatly impacts its weight capacity. Larger wheels are capable of accommodating heavier loads due to their ability to distribute the weight over a larger surface area. This not only helps in supporting more weight but also minimizes the stress exerted on floors, which is especially important when transporting heavy items over sensitive surfaces.
Moreover, larger wheels tend to roll more smoothly across different types of flooring and can more easily overcome obstacles such as debris and thresholds. This ease of movement reduces the rolling resistance and the amount of effort required to move heavy loads.
Load Distribution Among Casters
Even distribution of weight across all casters used on a piece of equipment is critical to prevent overloading and potential caster failure. Design considerations should include the placement and quantity of casters as well as the design and shape of the equipment to ensure that the center of gravity of the loaded equipment remains central among all the casters when moved.
Uneven distribution can place undue stress on one or more casters, leading to premature wear or even catastrophic failure. In scenarios where the load cannot be evenly distributed because of the equipment’s design or center of gravity, caster selections with higher load capacities can be used strategically to accommodate the uneven weight distribution.
Understanding these aspects of load capacity allows for informed decision-making when selecting casters for any application, ensuring safe and efficient operation.
Factors Affecting Caster Load Capacity
The ability of a caster to support weight is not solely dependent on its load rating; several other factors play a vital role in determining the overall load capacity. These factors must be carefully considered during caster selection to ensure optimal performance and longevity. Let’s explore the primary elements that influence a caster’s load capacity.
Material Construction
The materials used in the manufacturing of casters are fundamental to their load-bearing abilities. Various materials offer different levels of strength, durability, and resistance to conditions such as impact, abrasion, and exposure to chemicals:
- Aluminum: This metal is lighter than steel and resistant to corrosion, making it suitable for environments where rust is a concern. Aluminum casters can support substantial weight, though generally less than steel.
- Plastic: Plastic casters are lightweight and won’t rust, making them ideal for light applications and clean environments, like medical facilities. However, they usually have a lower load capacity compared to metal casters.
- Rubber and Polyurethane: These materials are often used for the tread of the wheels to provide floor protection, noise reduction, and some cushion for the load. They may have a lower load capacity but can absorb shock and vibration effectively.
- Steel: Known for its strength and durability, steel is often used for heavy-duty casters. It can support high loads and withstand harsh conditions, though it may not be as gentle on sensitive floors.
Wheel Diameter and Width
The dimensions of a caster wheel significantly impact its load capacity:
- Wheel Diameter: Larger wheels allow for easier rolling and can handle heavier loads. They are better at distributing the weight across a larger area, which decreases the stress on the wheel and the floor.
- Width: A wider wheel tends to distribute the load better than a narrow one. This can lead to increased load capacity, improved stability, and reduced wear on the wheel material.
Caster Bearing Types
Bearings are a critical component of casters as they facilitate movement and handle the stresses exerted during rolling:
- Plain or Sleeve Bearings: These are simple and cost-effective, ideal for light loads and infrequent movements. Sleeve bearings have minimal moving parts, making them quieter and easier to maintain.
- Ball Bearings: Designed for heavier loads and more frequent use, ball bearings reduce friction and make it easier to start and maintain rolling with heavier weights. They are also more durable under demanding conditions.
- Roller Bearings: These are great for applications that require moving heavy loads at moderate speeds. They typically handle higher loads better than ball bearings and produce less friction. When selecting casters, the material construction, wheel dimensions, and bearing type all play crucial roles in the caster’s ability to carry a specific weight, roll smoothly, and last for an extended period. These factors contribute to the efficiency and safety of caster-equipped items, influencing both their immediate performance and their maintenance over the long run.
Calculating the Right Caster for Your Needs
Choosing the correct caster for your application is critical to ensure the safety and longevity of both the casters and the equipment they support. Accurately determining the total load, selecting the correct caster, and considering safety margins and load testing are essential steps in this process.
How to Determine Total Load
To select a suitable caster, you must first calculate the total load that the casters will need to support. This load is the sum of the weight of the equipment itself plus any additional weight it will carry during operation, including:
– The weight of the equipment or furniture before any load is applied.
– The maximum weight of the cargo, goods, or additional components that the equipment will carry.
– Any dynamic forces that may occur during use, such as the force exerted when the equipment is pushed or pulled.
It’s important to consider the worst-case scenario in terms of load to ensure that the casters won’t fail when they’re needed most.
Selecting the Right Caster Based on Total Load
Once the total load is determined, the next step is to choose a caster that can handle that weight. It is crucial to select a caster that has a load rating that meets or exceeds the total calculated load. Remember to consider the number of casters that will be used and divide the total load by the number of casters to determine the load per caster.
For example, if the total load is 400 pounds and you are using four casters, each caster must support at least 100 pounds. However, it is advisable to choose casters with a higher load rating than the minimum required to ensure reliability under all conditions.
Safety Margins and Load Testing
Incorporating a safety margin into your load calculations can provide extra assurance against unexpected overloading or uneven weight distribution— factors that are often overlooked but can lead to caster failure. A common practice is to add a safety factor of around 25-30% to the total load when selecting a caster.
Additionally, routine load testing of the casters in their specific application can help determine whether they are still operating within their safe load-bearing range or if they’re being pushed beyond their limits. Load testing can also reveal potential issues with caster performance before they lead to equipment damage or safety hazards.
Choosing the correct caster involves these detailed calculations and considerations, ensuring that the equipment can be operated safely and efficiently while extending the lifespan of the casters.
Case Studies: Casters at Work in High Weight Applications
Casters are integral components across numerous industries, adept at handling heavy loads and ensuring smooth transportation of goods and machinery. Here we delve into specific case studies that showcase the efficacy of casters in diverse high weight applications.
Industrial Environments
In industrial settings, casters are often subjected to extreme conditions, including heavy loads, high-impact forces, and harsh operational environments. For instance, a manufacturing plant may utilize heavy-duty casters made of forged steel with polyurethane tread for transporting heavy machinery or parts. These casters must be robust enough to carry loads that can exceed thousands of pounds while maintaining maneuverability and protecting industrial flooring from damage.
A real-world example involves a well-known automotive manufacturing company that implemented specially designed heavy-duty kingpinless casters on their engine assembly line carts. This upgrade facilitated the transport of substantial sub-assemblies with ease, improving their operational efficiency and worker safety.
Medical Facilities
Medical facilities may not seem like high-weight applications at first glance, but the need for reliability and precision in these sensitive environments makes caster selection crucial. Operating room tables, patient transport carts, and heavy diagnostic equipment like MRI machines require specially engineered casters that can handle significant weight, maintain hygiene, and offer quiet operation.
Case in point, a large hospital recently transitioned to stainless steel casters with non-marking, antimicrobial wheels for their patient transport systems. These casters are designed to support the weight of the bed and occupant, maneuver smoothly over various surfaces, and withstand rigorous cleaning protocols.
Heavy Machinery
Heavy machinery such as construction equipment, agricultural machinery, or large-scale industrial appliances often require custom-designed casters that can handle the excessive loads and uneven terrain. These casters are typically constructed from high-grade steel with large diameters and wide treads to distribute weight efficiently and reduce ground pressure.
For example, a construction company might use pneumatic or semi-pneumatic casters on their mobile compressor units. The cushioning effect of the air-filled tires allows the heavy compressors to be moved over gravel, dirt, and uneven surfaces at the job site without jarring the equipment and without the danger of a flat tire associated with traditional air-filled tires.
Through these case studies, we can appreciate the versatility and importance of correctly selecting and implementing casters for various high-weight applications, ensuring reliable performance in industrial facilities, medical centers, and when operating heavy machinery.
Summary
Understanding caster load capacity is crucial for safe and effective caster selection. By carefully considering factors like material, wheel size, load distribution, and using a calculated safety factor, you can ensure your equipment performs reliably. Choosing the right caster helps protect your investment, equipment, and operators, guaranteeing smooth and safe mobility in various applications.